Annapolis Post Office
We welcome you to explore the construction services that NPB has to offer.
Annapolis Post Office
North Point Builders was the General Contractor for the Annapolis Post Office historic renovation. The goal of the adaptive reuse project was to transform the vacant and outdated building into functional modern offices for the State of Maryland.
The 3-story Annapolis Post Office building was originally constructed in 1901 as a terra cotta structure. Both the exterior and interior spaces display the elegant and ornate Georgian Revival architectural features that were popular during that time. Additions were later erected in 1926 and 1939, the latter being a 2-story concrete structure. With the building standing vacant for several years, the State of Maryland decided to renovate the old post office to house offices for the Secretary of State, Governor, and support and administrative staff.
The project was a comprehensive renovation of the ground, first, second, and attic floors totaling 25,000 SF. Interior historic spaces, existing millwork, and exterior stone and metal elements were part of an extensive restoration process to preserve the building’s unique architectural elements. The restored historic elements included extensive lobby millwork, wood doors, wood trim, wood flooring, plaster walls and ceilings, plaster cornice trim, metal railings, granite and marble stone, post office boxes, and light fixtures. In addition, all new mechanical, electrical, and data systems were installed to bring the building up to modern standards.
Owner | Maryland DGS |
---|---|
Location | Annapolis, MD |
Services | General Contracting |
Portfolio Type | Offices Historical Restorations |
Modern Transformation Challenges
The juxtaposition of historic restoration and modernization distinguishes the Annapolis Post Office from all other projects. Aside from restoring 100-year-old elements of the building, the success of the project also hinged on installing brand-new mechanical, electrical, and fire protection systems. Of course, the post office’s early 1900’s structures didn’t account for these modern systems in their design because these systems didn’t yet exist! The construction methods used in original structures are no longer used for modern standards and therefore, not well known by many craftsmen. With no drawings to show structures behind existing finished wall surfaces and limited space for system components, the project team readied themselves for an uphill battle.
The project’s design intent required that all mechanical, electrical, and fire protection infrastructure be concealed within the historic walls and ceilings. To understand the layout for the new systems, the team investigated subsurface conditions by opening walls and ceilings in critical areas to accurately assess the situation. Based on the investigation, a layout plan was strategically developed to route all piping and duct work through the confines of the existing historic building while maintaining the structural integrity.
The project team pinpointed precise areas where duct work, piping, and electrical conduit would penetrate existing floors, walls, and ceilings to determine the structural makeup of each location. Then, NPB, the infrastructure contractors, and structural engineer collaborated to develop reinforcement details for each penetration. Due to the varying conditions throughout the project, no two penetrations were alike. There were several locations where the openings cut out of the historic plaster revealed large existing steel beams. In these cases, the utilities were rerouted to accommodate the existing structure, keeping the project moving forward with minimal impact to time or cost.
Overall, the mechanical, electrical, and fire protection systems were exceptionally and methodically installed. Any obstacle that came in the way – sometimes even literally – the entire project team adapted with resourceful solutions and open collaboration. When incorporating the new complex infrastructure, the team persistently preserved the project’s goal to acclimate the historic space to today’s technology standards and current user needs.
Historic Restoration and Adaptation
The restoration of 100-year-old elements and adapting them to the facility’s design and user intent brought on unpredictable challenges throughout the entire project. Everyone involved – from the stakeholders to the designers and builders – had to become a united team to overcome these obstacles and unforeseen conditions. Specifically, the work associated with the historic features of plaster, millwork, and stone, encountered an extraordinary number of difficulties throughout the project.
Plaster Predicament
The exact plaster scope of work was not clearly defined in the contract documents. Both the quantity of plaster restoration (as a result of existing conditions) and the quantity of plaster patching (required for new mechanical, electrical, and plumbing rough-in’s) was unidentifiable. The original unit price allowance accounted from 1,200 SF of plaster restoration work. Due to many unanticipated issues, that number extended to over 21,500 SF of total plaster work.
During the demolition phase, lead and asbestos were discovered in existing plaster ceilings which were initially identified to remain. Based on the large quantity of work required in these plaster ceilings, the State decided to abate all plaster containing lead and asbestos. The original unit price allowances for plaster did not account for any plaster restoration on the ground floor. As a result, over 12,500 SF of new plaster ceilings were installed at the ground floor following abatement.
Then as work began on the first and second floors, it became apparent that the unit price allowance for mechanical, electrical, and plumbing rough-ins in plaster walls was underestimated. The design team originally estimated quantities for this work by utilizing the shortest distance required to add infrastructure components. However, upon removing plaster for new infrastructure, it was determined the shortest distance could not be utilized due to an exorbitant number of unforeseen obstructions within the wall assembly. To ensure the project would continue at an accelerated rate, the plaster contractor coordinated their redefined scope of work around the MEP contractor’s schedule so both rough-in and plaster could be completed simultaneously.
Although the quantity of new and historic plaster work drastically increased, the entire project team faced the challenge head-on. By increasing manpower and fostering a team-oriented approach, the necessary extra plaster work progressed steadily and was completed with the utmost quality.
Millwork Mania
Before any work could start, the State, design team, NPB and millwork refinishing contractor completed field assessments to determine the location, quantity, and type of restoration needed. Once the type of restoration was identified, the millwork contractor prepared multiple mock-ups of sanding, stripping, surface repairs, partial replacement, full replacement (with Dutchman repairs), stain color, and final sheen for approval by the State. Matching the grain, color, and sheen was only a portion of the necessary mock-ups. As mock-ups progressed, several more unforeseen challenges were encountered.
Over the years, millwork maintenance added multiple layers of finish. This created a reaction between the existing and new finishes, resulting in bubbling, cloudiness, and peeling of the new finish. Many different test processes were completed to eliminate these reactions and allow for new finish to be unblemished and consistent with existing finish.
During the mock-up phase, the approved color match was intended to be used throughout the whole project. However, due to the aging of the wood and varying sun exposure it became evident that multiple color selections and sheen were necessary to aesthetically tie the old and new finish together within individual spaces.
When it came time for the crews to begin the restoration work, the building humidity levels were not ideal. This delay was a result of many unforeseen conditions related to coordination issues for integrating the new mechanical, electrical, and data systems within the walls of the historic finishes. There were also delays with the startup of the air handling units associated with a setback by BGE providing new permanent service to the building. Even after the building was temperature controlled, it took longer than anticipated for the building humidity to acclimate to a level required for the historic wood restoration.
Eventually, the conditions were ideal for the millwork crews. To accelerate the delayed work and maintain the highest level of quality, sufficiently sized and exceptionally skilled crews were provided to push the project forward. Overall, the historic stained woodwork restoration was accomplished successfully, resulting in the undeniable beauty and eloquent harmony of original and restored wood finishes.
Stone Shortage
One of the most unique and adaptive elements of design was the recycling of marble toilet partitions for wainscoting. The original 1901 partitions were spaced out throughout the building. This created an abnormal challenge because the marble slabs needed to fit cohesively together to achieve the wainscoting design. These slabs were not meant to fit together as one piece, so the stone contractor was tasked with the challenge to create a consistent look for the wainscoting. Naturally, the stone varied in color and grain detail. The stone contractor performed a detailed analysis to ensure the best quality match was achieved when aligning slabs together.
When the original design was compared to the usable amount of historic stone, there was not enough historic stone to meet the design’s requirements. The design team and stone contractor collaborated to modify the design in a way that ensured the available materials would follow the design intent as closely as possible. Once the design was finalized, the large slabs of stone were removed, cut, repaired, and reinstalled. This material was irreplaceable, leaving absolutely no room for error. Thanks to the exceptional skills of the craftsman, the result is an aesthetically pleasing layout of the historic marble stone.
Schedule A Consultation To Discover What We Can Do Together.
View Other Projects
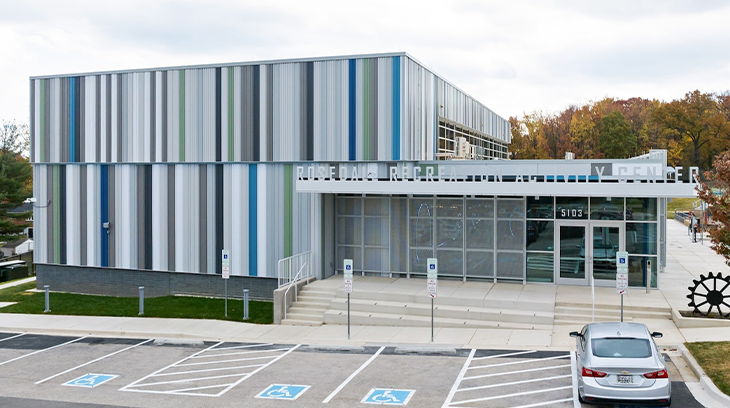
Rosedale Recreation Activity Center
North Point Builders provided General Contracting Services for the Rosedale Recreation Activity Center, a 15,000 SF multi-use facility created to offer a range of recreational and social amenities.
Read More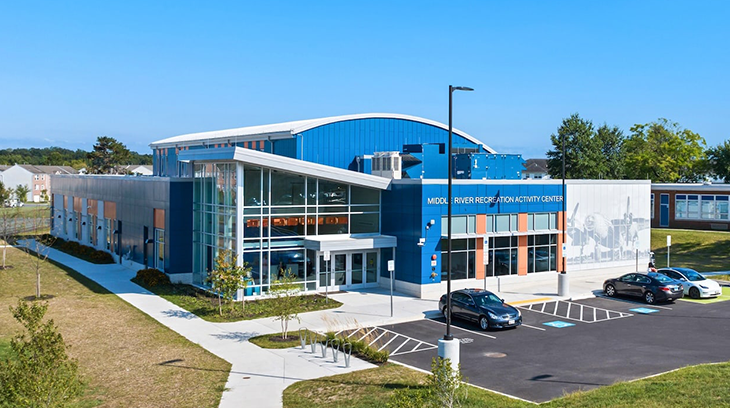
Middle River Recreation Activity Center
North Point Builders provided General Contracting Services for the Middle River Recreation Activity Center, a new one-story, 15,000 SF facility to provide recreational and multipurpose spaces for the…
Read More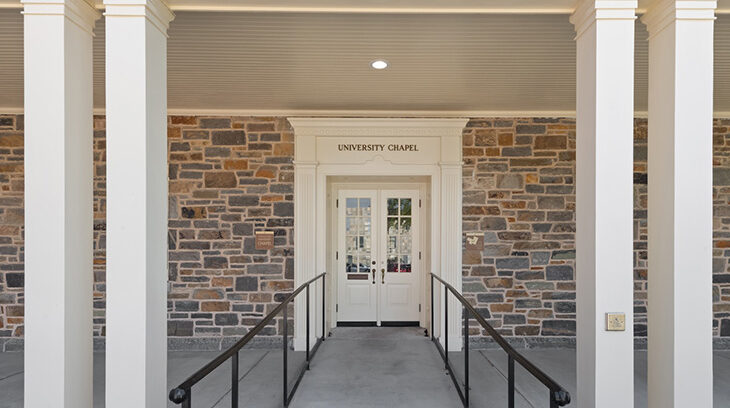
Morgan State University Memorial Chapel Window Restoration
North Point Builders served as the General Contractor for the window restoration of the historic Memorial Chapel at Morgan State University in Baltimore, Maryland. A key landmark on…
Read More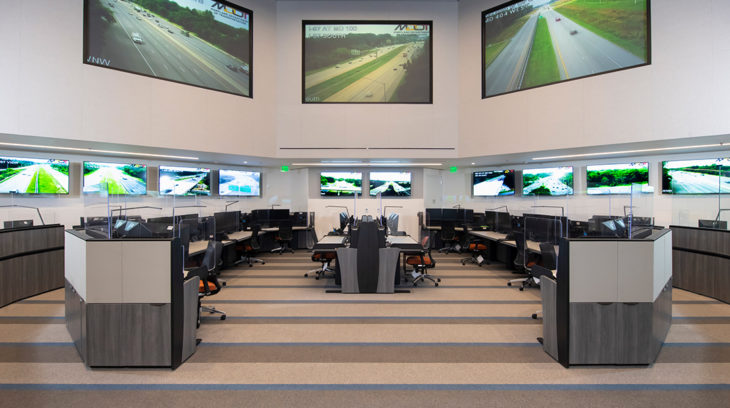
MDOT SHA Statewide Operations Center
North Point Builders was the General Contractor for the MDOT SHA Statewide Operations Center reconfiguration and renovation project. The purpose of the SOC Floor Reconfiguration project was to…
Read More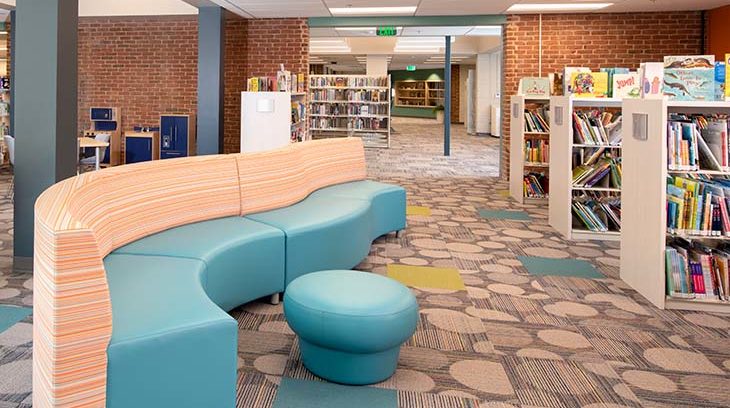
Reisterstown Library
North Point Builders provided General Contracting services for the renovation of the Reisterstown Public Library Branch in Reisterstown, Maryland.
Read More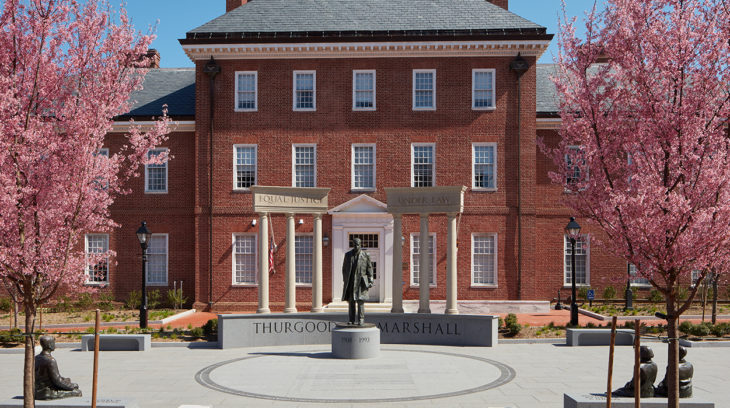
Lawyer’s Mall Historic Courtyard
North Point Builders provided General Contracting services for the Lawyer's Mall historic courtyard renovation.
Read MoreHoward County Bain 50+ Center
North Point Builders provided Pre-Construction and General contracting services for the renovations of the Bain 50+ Center in Howard County, MD.
Read More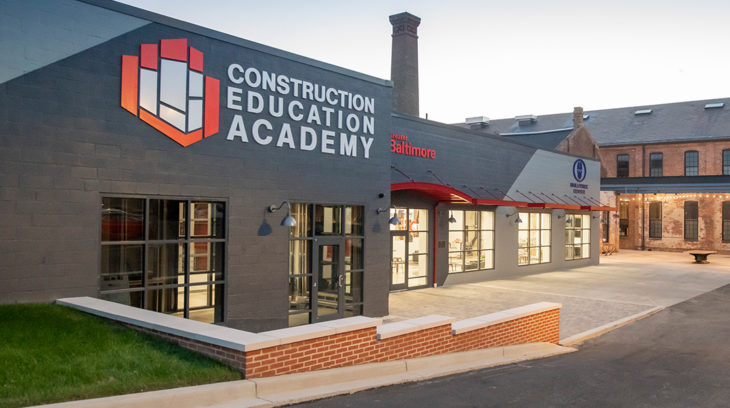
Construction Education Academy & Offices – ABC Greater Baltimore
North Point Builders was the Construction Manager for the Associated Builders and Contractors of Greater Baltimore’s (ABC) new Construction Education Academy and Office Headquarters. The new academy provides…
Read More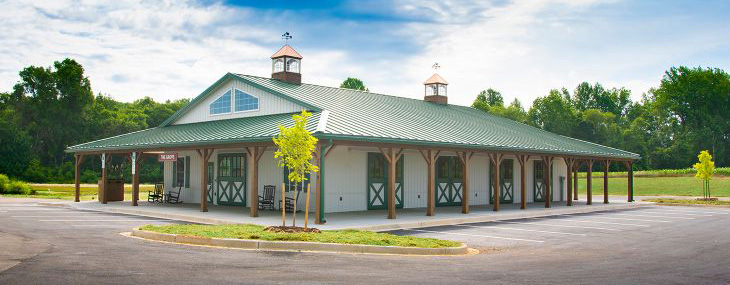
Harford County Agricultural Center – The Grove
North Point Builders was the General Contractor for the construction of the new Harford County Farmers’ Market – The Grove. Harford County’s vision to consolidate and promote agriculture…
Read More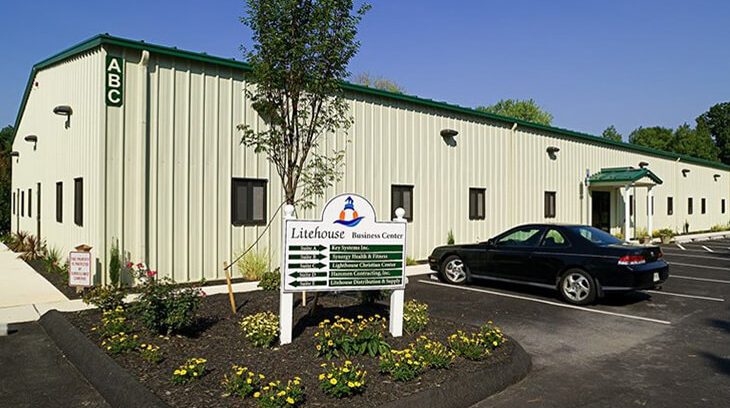
Key Systems Offices
North Point Builders was the Design-Build Contractor for the Baltimore County Recreation and Community Center. Located in Jacksonville, Maryland, the building was part of a larger park development…
Read MoreBring Your Project To Life
Schedule a consultation to discover what we can do together.
Meet with us to discuss your project needs.
Create a blueprint to meet expectations.
Enjoy the final outcome of a successful project.
$750M
Projects Managed
30+
Years Experience
50+
Building Awards Won
Get In Touch
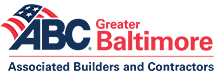
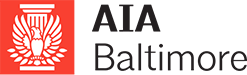
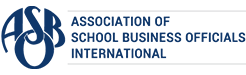
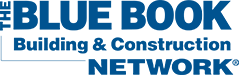
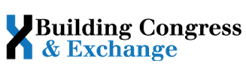
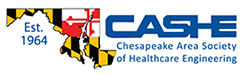

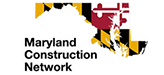

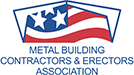